AUTOMATION
Automation has been mentioned briefly in the Longwall section of the Fundamentals of Coal Mining module of this web site. Progress has been made in Australia in many aspects of automation, largely as a result of research initiatives under the auspices of ACARP's Longwall Automation Steering Committee, carried out by CSIRO and CRC Mining in co-operation with Original Equipment Manufacturers (OEMs) and operating mines. The research has been/is being carried out in ten sections(1):
- Face alignment, focusing on lateral direction control and face geometry.
- Horizon control looking at maintaining cutting horizons as required by the mining process.
- Open communications by developing open architecture between systems hardware and software components.
- OEM involvement/commitment by creating mechanisms for exchange of information between the project team and equipment manufacturers.
- An information system consisting of a monitoring station, automatic sequence design and operator displays.
- Production consistency and reliability focusing on condition monitoring and reliability, and then on optimising coal flow and finally on collision avoidance between components.
- Determining the redefined functions of face operators and subsequent training requirements.
- An implementation plan for introducing automation system components at strategic selected sites.
- A commercialisation plan for transferring the proven automation technology to the industry.
- A progressive automation implementation plan for all longwall mines in Australia by identifying the status of their existing technical specifications and the potential to implement appropriate levels of automation.
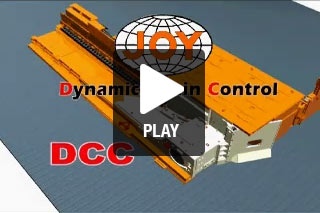
Description of an automatic AFC chain tensioning arrangement...
Duration: 04:02, Size: 11.5Mb
Video Courtesy of Joy Manufacturing Company Pty Ltd
Trouble viewing video? Download: .wmv or .mp4
It is obvious from the above that this is a very ambitious program and complete success in all aspects by the planned completion date suggested in some ACARP publications is unlikely. Further research is likely to be required in some areas while good progress has already been made in others. Putting all aspects together to create a fully functioning automatic longwall operation is also likely to be challenging and piecemeal progress is more likely (and is in fact occurring now, as most existing longwalls have extensive monitoring arrangements and some aspects of automation are already in use, or at least available).
One result of increased automation will be changes to the qualifications of the operating crews. While the traditional electrical and mechanical skills will still be required there will be an increased requirement for electronic and IT expertise on a regular basis. Alternatively, changes to equipment make-up and equipment fault self-diagnosis may result in fault correction merely involving changing out plug-in modules as instructed by the machine diagnostic system and fewer personnel with electronic qualifications will actually be required on site. The replaced item may be discarded or repaired elsewhere.
While automation should, in theory, reduce the need for skilled mining operators while operating normally, it is considered the need for such personnel will remain unchanged, at least in the near future. An automated face probably will not be able to recognise all changing conditions and the skilled mining operators will still be required to recognise when changes to the automated program are required to avoid loss of control or to prescribe the actions required if control is lost.
Progress on the ACARP project is available from ACARP sources but has been well summarised by Mitchell(1). Most information on progress on automation is available from other sources, such as the several hyperlinks listed below:
- LASC Longwall Automation Steering Committee – reports from Longwall Automation Steering Committee
- Landmark Longwall Automation Project (Profile - Project) – CSIRO report on Longwall Automation Project
- http://www.longwallautomation.com/docs/2003HPMPAachen.pdf - Paper by M Kelly,D Hainsworth, D Reid & H Gurgenci on work on the automation project
- http://www.eng.uq.edu.au/typo/fileadmin/filestore/aecn/longwall_automation_presentation.pdf - presentation of paper by D Hainsworth on automation
- http://www.australiancoal.csiro.au/pdfs/kelly.pdf - paper by M Kelly, P Lever, D Hainsworth, H Gurgenci & R Dubois, entitled "Longwall Automation: Are We Ready For Success?"
- http://www.lascautomation.com/docs/FaceAlignmentSpecificationV2.04_000.pdf - paper on roof support system communication and functional specification for face alignment
- ACARP – listing of ACARP projects; reports may be purchased or available to specified organisations
- http://www.minerals.org.au/__data/assets/pdf_file/0003/30459/SA08-07-Operator-crushed-between-longwall-roof-support-and-AFC-pan-line.pdf - example of a longwall hazard not solely related to automation but the risk is possibly increased by automation, even partial automation
- Topic of the Month – CSIRO comments on Longwall Automation Projects (this may be a short term web site).
- LASC Longwall Automation Steering Committee Description of the ACARP sponsored longwall automation LASC Longwall Automation project.